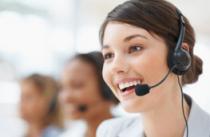
HKA's series of leak testers have traditionally provided failure information by showing an '*' followed by a letter. This section helps to illuminate possible causes and troubleshooting steps.
The final leak reading was less than the set limit
Common Causes:
- Leak in reference part
- Block reference port and retry test
- Invalid calibration
- Previous calibration was performed with a leak in the system
When entering into the READ phase a positive slope was detected. In direct flow models this indicates being over filled.
Common Causes:
- Too much time given during 'Fast Fill'
- 'Fast Fill' regulator set too high
- Pressure drop to part is too great to effectively stop fill cycle before being over pressure
Unit received the abort signal
Common Causes:
- A voltage bias across pins 9 and 12 of 12-pin connector
At the end of test the block test was performed. The pressure reading was not lower than the pressure limit after the set amount of time
Common Causes:
- Part is blocked
- Confirm with known good part
- Blockage in seal
- Add roll-pin or some means to avoid 'folding over'
- Crimped air line from tester to part
- Known good part will also fail
During the calibration the SystemZero could not be calculated with confidence as the sensor input varied too greatly
Common Causes:
- Seal movement
- Add a hard stop for seals
- Change seal durometer
- Add a wait before sending the start signal after sealing
- External air source
- Ensure that process air is not leaking through a valve into the test circuit
- Part still exhausting from previous test
- Try again after waiting
During the READ phase of the test, the slope was too large in the negative direction
Common Causes:
- Insufficient time for accurate test
- Extend times for STAB or READ
- Movement of seals
- Add hard stops for seals
- Temperature effects
- Add more cooling time or active cooling
After 1 minute the pressure sensor is reviewed and is expected to be close to the programmed zero. If not, the unit will not permit a test to start unless the pressure has been brought to zero or the unit has been tared.
Common Causes:
- Part still clamped
- Pressure sensor zero calibration has floated too high
- The unit must be zero'd either by a tare or pot adjustment
The flow reading was much larger than expected during the STABilization state
Common Causes:
- Gross leak
- Check seals for debris or damage
- Check the tubing from the test part to the leak tester for damage
- External air source causing flow
- Ensure control air is not leaking through a valve
The raw flow before a test has started was too far away from SysZero
Common Causes:
- An external air source
- Ensure a valve controlling test air paths isn't leaking control air
- Part still exhausting from previous test
- Wait and try again
The test failed the secondary pressure decay check
Common Causes:
- Leak in part, seals, or test lines
Calibration Zero Error
This happens when F Zero is much different than SysZero
F Zero: "Flow Zero" is calculated during a calibration and is the average of the final two 'Zero' readings
SysZero: "System Zero" is sensor zero when the leak tester is unpressurized
For versions 7 and earlier the difference cannot be larger than 500. For versions 8 and later the difference cannot be larger than 8000
Possible Causes
Typically this is caused by invalid 'Zero' readings due to a leakage. Possible root causes include:
- Hole in reference part
- Loose fittings or connections to either reference or test part
- A valve (internal or external) leaking control air into the test circuit
- Seal movement during the READ phase
- Leaking seal
- Bad part used during calibration
The pressure decay reading during calibration was much larger than allowable
Common Causes:
- Leak in part, seals, or test lines
- Ensure that the part is a good part
- Ensure seals are okay, free of debris or damage
The two pressure decay readings were too different from each other
Common Causes:
- Seal movement
- Ensure stand air is isolated from 'hungry' air consumers
- Use hard stops for seals
- External air source
- Usually observed in raw flow readings as well as a large leak
- Part still exhausting from previous test
- Check exhaust path to ensure air exits quickly
The reading taken during COMPensation time was too negative to perform a valid test (Only with 'Temp Comp')
Common Causes:
- Part temperature too cold for unit to compensate
- Allow more time for part to climatize or add active cooling
The reading taken during COMPensation time was too large to perform a valid test (Only with 'Temp Comp')
Common Causes:
- Part temperature too hot for unit to compensate
- Add cooling time or active cooling
- Seal creep during COMP reading
- Extend COMP time
Pressure halfway through STABilization was outside the bounds set by PRESSURE HI and PRESSURE LO in the part SETUP
Common Causes:
- Gross leak usually in seals, part, or test lines
- Check seals and part for large leak
- Wrong test program selected
- External program selection may not be enabled if the stand normally changes part number. Check setting in SYSTEM SETTINGS
- Incorrect settings
- Verify that settings for upper and lower limits are correct for test pressure
- Upstream pressure is insufficient
- Ensure pressure to leak tester is greater than required test pressure
- Check tubing from tester to pressure source for kinks or significant holes
The initial flow test was completed and failed. Sufficient flow was not read after a set amount of time
Common Causes:
- A blockage exists in the tested part
- Verify system with known good part
- A blockage or kink exists in the tubing between the leak tester and part
- Examine tubing leading from fixture to tester
- A blockage or kink exists in the tubing between the pressure source and leak tester
- Examine tubing leading from tester to supply port
- If initially setting up, parameters may be too stringent
- Change limits to reflect nominal part response
The span readings (CAL1 & CAL2) were too close to the zero readings (ZERO1 & ZERO2) in relation to the difference in zero readings
Common Causes:
- Insufficient time for accurate test without a drain valve
- Add a drain valve
- Control a seal cylinder from the leak tester EXH port
- Add time to STAB or READ
During the READ phase of the test the slope was too large in the positive direction
Common Causes:
- Insufficient time for accurate test
- Increase READ or STAB timers
- Ensure no kinks in line from leak tester to parts
- Movement of seals
- Add hard stops for seals
- Increase sealing pressure
- Try another seal durometer
- Temperature effects
- Wait for part to climatize
- Add temperature compensation
- Add active cooling
Vacuum pressure was not achieved to the set level after the VAC1 state
Common Causes:
- A gross leak either in the part or seal
- Ensure seals are clean and not damaged. Replace as required.
- Insuffient seal pressure
- Increase sealing pressure
The 24V power supply has dropped below acceptable limits
Common Causes:
- Insufficient supply voltage
- Ensure power supply rating is correct for application
- External source drawing high current
- Disconnect external loads to see if condition persists
A cross cooler test was completed and the flow or pressure was greater than the set limit after the set amount of time
Common Causes:
- A leak exists connecting two separate cavities within a test part
- Check manufacturing process
During a calibration the zero readings (ZERO1 & ZERO2) were too far apart
Common Causes:
- Insufficient time for accurate test without a drain valve
- Add a drain valve or control a seal motion using EXH port of leak tester
- Increase STAB or READ timers